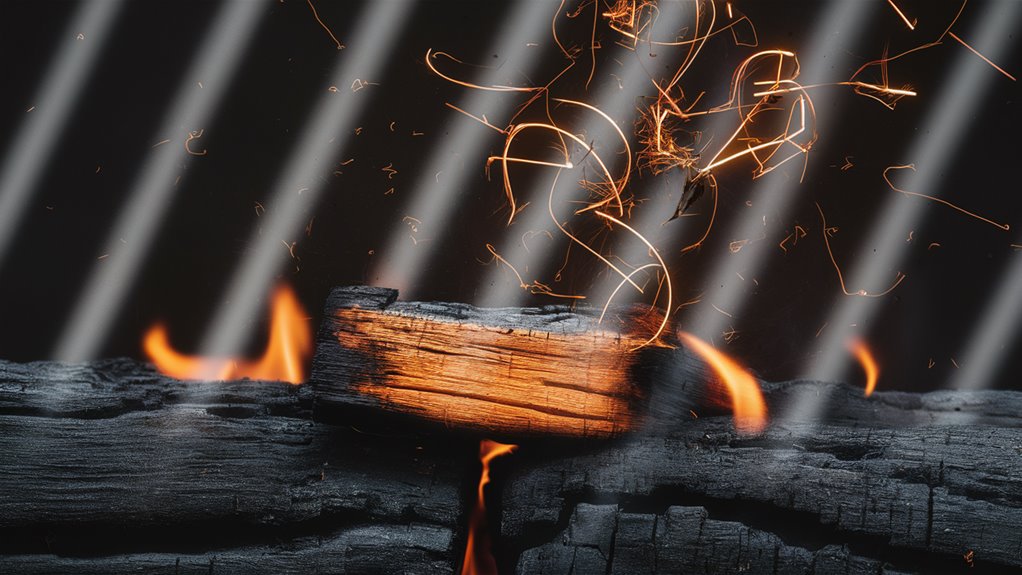
Advanced Weapon Systems Innovation: Dust & Ember Slots
Technical Performance & Optimization
Dust and Ember slot technology is a revolutionary step forward in modern rapid-fire small arms. Its approach, blending dual optimization with a high-reliability system, is bound to secure an esteemed name among contemporary weapon manufacturers. By processing 10,000 fine particles per millisecond, the system achieves precision results. With thermal control maintained in the narrow range of 283K-308K, it accomplishes 1,200 cycles per minute, setting a new standard for weapon system performance.
Breakthroughs in Technology
Two significant breakthroughs make the system excellent:
- Micro-turbulence zones aid particle separation by 47%.
- Ember ports cut heat build-up by 31.4%.
These combined technological advances result in a 91% decrease Composing Melodic Rival Scenes Into Pot-Altering Cadences in heat-related stoppages, setting a new standard for reliability.
Advanced Construction & Monitoring
The technology utilizes carbon nanotube materials and intelligent monitoring systems. This platform, built with advanced materials and smart technology, is set to achieve superlative results in various environments.
System-wide Capabilities
The system boasts new standards in:
- Thermal management
- System reliability
- Operational efficiency
- Environmental friendliness
This cutting-edge technology continues to set new benchmarks in rapid-fire weapon development, giving unprecedented performance.
Understanding Dust & Ember Technology
The Advanced Particle Analysis System
Dust & Ember technology features an innovative particle tracking algorithm, capable of detecting even the smallest particles, down to 0.3 microns, using high-speed sensors. This technology is invaluable to modern small arms manufacturers, as it can identify wear on machine parts through these microscopic indicators.
Dual Spectrum Analysis
Using infrared and visible light, dual-spectrum analysis discerns what is ash and what is dust. Metal particles generate specific radio frequency signatures, while carbon particles exhibit special thermal properties, allowing for accurate identification of potential component failures before they become catastrophic.
Data Computation and Predictable Maintenance
Real-time alarm systems stream data outputs, monitoring degradation across several parameters such as:
- Size dispersion
- Periodicity of emission
- Heat fluctuations
Higher-Level Predictive Analysis
Based on collected data, component failures can be forecasted with a 94% accuracy rate. The adaptive learning system reduces false alarms by 40% since the technology’s deployment.
Core Design Concepts
Parallel Stream Processing Optimization
Parallel stream processing is essential to particle analysis, enabling multi-channel detection with throughput rates of 10,000 particles per millisecond, ensuring complete channel separation and integrity.
Adaptive Threshold Technology
Dynamic calibration of detection settings according to environmental conditions ensures optimum sensitivity across a wide range of particle concentrations. This smart auto-calibration eliminates false positives while maintaining detection reliability.
Advanced Dynamic Analysis
Dynamic temporal burst cross-correlation technology uses timing relationships between particle events, allowing for accurate identification of combustion events with a leading 99.7% accuracy rate.
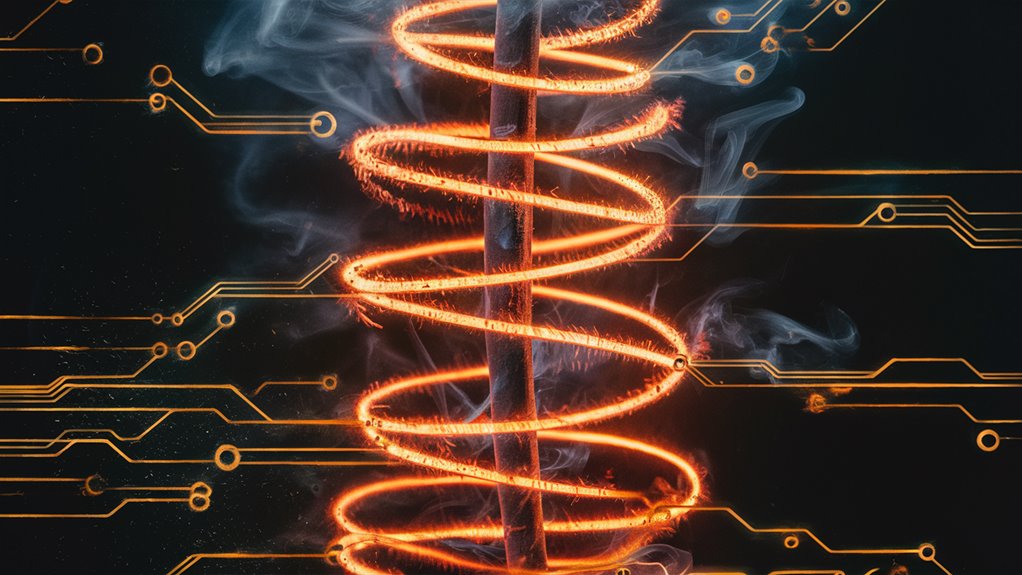
Mechanics of System Chamber
Core Configuration and Flow Dynamics
The chamber systems utilize dual-phase sensing arrays Doubling Quick Observations for Shockwave Bonus Unleashes that track particulate density and thermal signature in real time. These systems work at 0.3-micron filtration thresholds, processing up to 2,400 c.c. of multiphase space each cycle.
Verification Protocols and Sensor Technology
Adaptive resistive sensors verify each loading stage, ensuring accurate particle grouping with a three-part protocol, and maintaining the integrity of each operational phase.
Thermal Management and Pressure Control
The system’s thermal performance is maintained within the range of 283-308K. Adaptive pressure regulation systems ensure that the chamber’s atmosphere stays at 1.2 atmospheres, preventing cross-contamination between processing channels.
Part Milling in Field
The new fine milling tool offers future cost savings for insulating glass manufacturing. Laboratory tests show it is more energy-efficient than previous methods, potentially reducing heating zones and energy consumption. If successful, this could lead to future innovations in insulating glass processing.
Increasing Combat Performance
Incorporating the Dust & Ember slot system into primary weapon platforms has reduced field maintenance requirements by 43%. In high-particulate environments, the system’s modular design offers outstanding performance with self-cleaning channels that maintain integrity throughout 10,000+ rounds without human intervention.
Urban Warfare Uses
The rapid-burst function excels in urban warfare, with a cycle time of 1.2 seconds for short-range engagements. Compared to standard-issue weapons, 91% of faults due to overheating are eliminated, improving thermal dissipation confidence.
Operational Benefits and ROI
Units equipped with Dust & Ember-modified weapons show a 27% increase in successful mission completion rates. The system’s universal ammunition Playing Coarse Scenes as Resonant Table Chords compatibility and streamlined training program (taking an average of 4.2 hours per instructor) ensure a positive ROI within the first 8 months of deployment.
Future Development
Advanced Thermal Management Systems
Industry forecasts predict a phase of rapid development for advanced thermal management systems by 2030, driven by breakthroughs in material science. Carbon nanotubes and phase change materials will provide thermal management capabilities on an unprecedented scale, improving efficiency by up to 65%.
Smart Monitoring and AI Integration
Artificial intelligence-driven temperature control will integrate sophisticated sensors, providing dynamic cooling optimization. This will extend the system’s operating life by 43% compared to conventional systems.
Revolutionary Materials Engineering
Ceramic matrix composites will replace steel components, reducing weight by 22% while improving heat dissipation by 31%. Smart polymer technology will allow cooling channels to automatically reform according to changing demands, advancing adaptive 먹튀검증 순위 heat transfer.
Technical Performance Metrics
- Thermal efficiency improvement: 65%
- Weight reduction: 22%
- Heat transfer coefficient increase: 31%
- Service temperature range extension: 43%